Combustible Dust: How Concerned Should You Be?
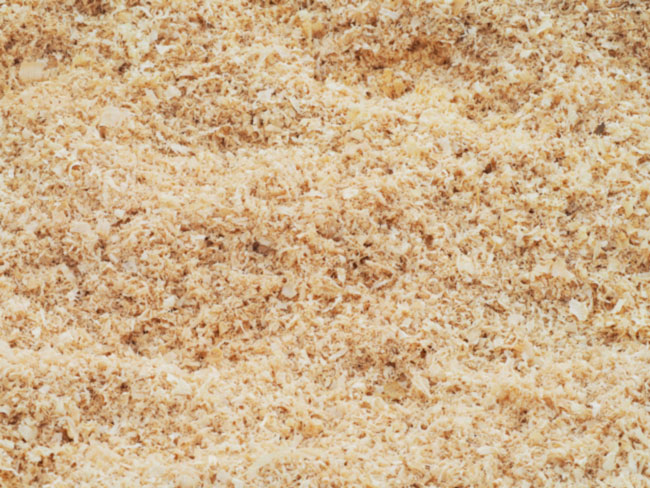
Have you ever taken a handful of sawdust and thrown it over a flame to see the wonderful display of fire and sparks dispersing through the air? The tiny shavings of wood ignite instantly and spread wildly and erratically as their state changes from inanimate and harmless to explosive and destructive. Now combine that imagery with your confined manufacturing based work environment where you are surrounded by millions of dust particles made up of things far more incendiary and complex than wood.
Combustible dust is as straightforward and dangerous as it sounds.
By definition, combustible simply means able to be burned easily and dust’s most basic definition is a fine powder from a particular substance which has tendencies to build up in buildings and on surfaces that have not been recently cleaned. While at home, dust on the top of a picture frame poses no threat, it can be cleaned with the swipe of a finger. However, in manufacturing settings, dust composed of countless properties can coat surfaces and hang in the air posing not only threats to one’s respiratory system, but, depending on the substance, give rise to dangers such as explosions and sweeping fires that threaten lives and infrastructure.
How dust can ignite
With combustible dust one deals with millions of minute particles all acting as a fuel ready to ignite. From there, only a handful of natural elements need to be present to create a fire or explosion: oxygen and a source of ignition which can be as simple as the correct amount of heat or something as small as a spark. From here, the explosion happens from dispersion and confinement, in essence, dust congregates as a mass in the air – no different than a cloud in a confined space with nowhere to go but out (boom) – and ignites upon reaching the proper temperature or introduction of a spark.
Yes, you read that right.
It is crucial to understand that when dealing with combustible materials one does not need a spark to create a fire or explosion; heat is sufficient. Byproducts of the manufacturing process can additionally enact a domino effect of combustion by being burnt and later introduced to the more dangerous environment by means as simple as wind, or, in a most basic stage, almost act like a line of gunpowder that can burn its path to a more destructive force should the environment not be kept clean.
More industries are affected by this than you would think.
If something doesn’t easily burn in a solid state this does not mean you are safe from its explosiveness as dust (aluminum or iron are just two examples). Elements found within wood, agriculture, metals, plastics, carbonaceous, and various other forms are risks for combustion when broken down to a dust state.
Reducing the risks
The easiest way to protect yourself starts with your eyes. You can see dust on objects, you can see it suspended in the air.
The next step is to ask what the dust is made of. How large are the dust particles? How is it being dealt with at the work sight? How is air flow, ventilation, what barriers are present that could trap flammable / explosive amounts of dust? What could ignite the situation?
In today’s day and age it could be as simple as a spark from plugging in your phone for a quick charge, a welding flame, stoves, or electrical equipment. Nothing should be overlooked as it is the “freak” accident that is never prepared for; be creative with your insight as the raw power of combustion is more than can be survived in the wrong setting and is not worth chancing.
Next, know what is being produced, handled, or worked with in the current setting and if you identify a combustible danger, take measures to remove its presence by means of Containing, Capturing, and Cleaning.
We’re not through yet.
Dust must not be allowed to settle in excess and should be dealt with constantly — eliminate and / or constantly observe horizontal spaces. Appropriate ventilation and electrical insulation is essential. General maintenance must be performed on all machinery.
In cases where dust and shavings are a direct byproduct of the manufacturing setting, DO NOT sweep or displace dust with an air hose, that simply makes it a problem somewhere else and for later. Dust must be vacuumed. In the cases of mass production technology, of dust extraction or collection equipment, such as baghouses, should be installed.
Having the correct equipment
Dust collection systems play a major role in reducing dusting in facilities and shops. Various systems that include ducts, filters and vacuums are utilized to remove dust hazards from the work space.
It is vital that the proper collection system be implemented in order for the largest amount of dust to be captured. This makes companies who custom design collection equipment all the more valuable.
If you’re not sure that your shop or facility is in need of a dust collector, contact one of our representatives today. Our top notch engineers can evaluate your facility’s needs and design a custom system to fit those needs.