Baghouse Ventilation System Design Mistakes to Avoid
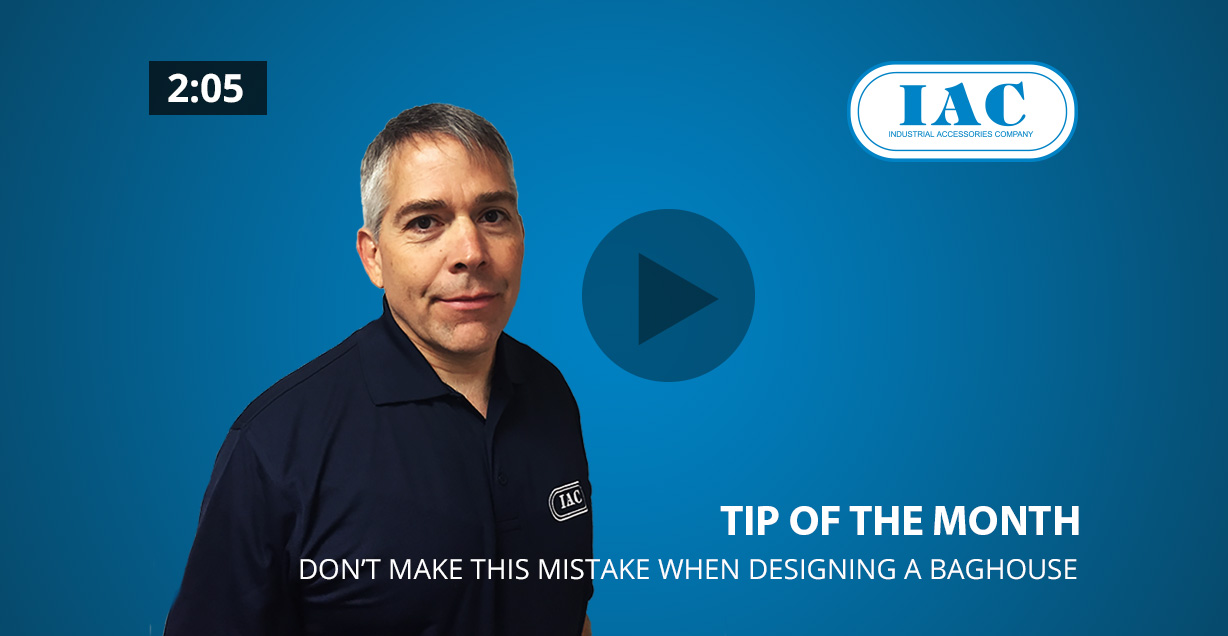
One of the biggest sources of operational problems in a baghouse dust collector's ventilation system is the initial layout.
When we say the initial layout, we mean the blank sheet of paper, or "paper napkin", stage of an industrial plant's equipment layout and ventilation system design. This phase of a project - before any engineering has begun - is the true first phase. Often, the problems with a baghouse dust collector's performance can be traced back to this beginning stage.
Baghouse Ventilation System Design Mistake #1 - Improper Placement of Fan
![]() |
![]() |
Poor Design: Air inlet is on the same side of the baghouse as the fan and dust discharge. | Improved Design: Air inlet on the same side of the baghouse as the dust discharge, with the fan on the opposite side. |
Looking at the drawing on the left, you can see that the fan and the inlet were designed on the same side of the baghouse as the air inlet. As you can see, the airflow (a.k.a. gas flow) doesn’t have much motivation to travel all the way to the other side of the baghouse. This will shorten the useable life of the baghouse's filter media closest to the air inlet, causing unnecessary maintenance labor time to fix, and increased compressed air costs in a pulse jet baghouse system.
Now compare it to the drawing on the right. Do you see the difference? When placing the fan at the opposite end of the inlet, you allow the airflow to travel throughout the entire system, creating a better balance for dust collection and ventilation.
Baghouse Ventilation System Design Mistake #2 - Improper Placement of Dust Discharge
![]() |
![]() |
Poor Design: Air inlet is on the same side of the baghouse as the fan and dust discharge. | Improved Design: Air inlet on the same side of the baghouse as the dust discharge, with the fan on the opposite side. |
Another design issue that people run into is placing the discharge valve on the same side as the inlet. When air flow (a.k.a gas flow) first enters a baghouse dust collector system it is at a high velocity. Because dust surrounds the discharge area, this dust begins to mix with the air (or gas) flow coming into the system, which results in re-entrainment. Similar to the issue with the fan, placing the discharge on the opposite side of the baghouse as the inlet can solve the problem of filtered dust mixing with the airflow.
The industrial ventilation system's airflow is better balanced, and the filtered dust can rest in an area that is not disturbed, allowing for improved performance of the baghouse system. Maintenance labor time, filter media, and compressed air is saved because the baghouse is not filtering the same dust over and over again.
IAC's baghouse design experts are here to help design dust collection systems to meet production rates and provide a long service life. Contact us today!