5 Helpful Baghouse Maintenance Tips
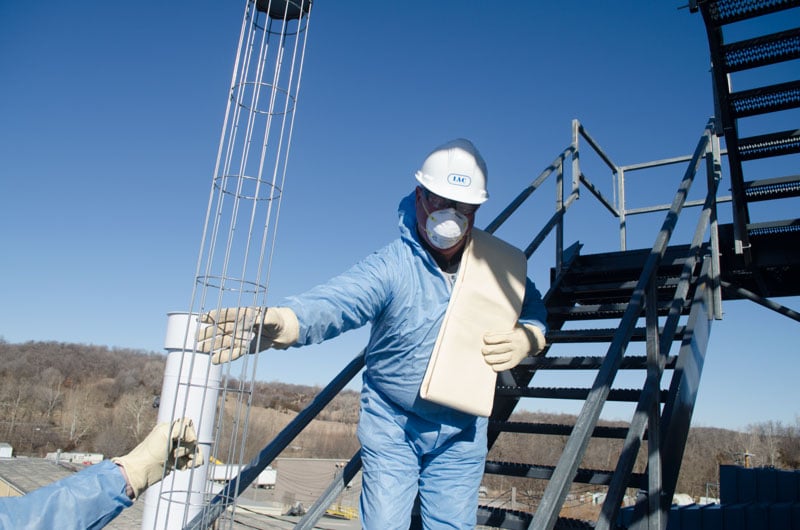
1. Ensuring a Proper Bag-to-Cage Fit
The fit between the bag and the cage is critical for filters to perform properly. Filters that are too lose or too tight will have severely limited collection efficiency and may fail prematurely. There are many different types of media, each with a different pinch “size” to look for when ensuring your pinch isn’t too loose or too tight. For instance, when inspecting a filter bag made of felt, a proper “pinch” should only be about .025”-0.5,” whereas a bag filter made of fiberglass or a ePTFE membrane would require a much tighter pinch (ranging from .0625”-0.375”).
2. Which Type of Filter Bag Would Be Most Applicable For Your Baghouse?
Choosing the correct filtration material for your process and dust collection needs is obviously a crucial element in terms of maximizing operational performance. There are several key criteria that one must consider to ensure you have the right filter for your application:
Maximum Inlet Operating Temperature
Always consider what would be the highest inlet temperature into the baghouse. This will immediately narrow your choices to the synthetic fibers that can withstand and operate in those ranges.
Inlet Grain Loading
An often overlooked factor is the amount of dust the system will see. Knowing your inlet grain loading/cfm will help a bag manufacturer determine the possible needs for durability and the type of fiber and possibly the weight of the filter bag.
Particle Size/Distribution by BOTH Volume and Count
Understanding the distribution size of material collected is critical in establishing the right filter media. Years ago, only particle size by weight was considered, and while that’s an important factor to consider, one must not overlook the importance of getting the distribution by size as well. For example, if you had 100 grains/acfm, and 99 of them were
Gas Stream Chemistry
It’s obviously important to understand whether the baghouse will be filtering particulate and gases that are chemically active (whether acidic or alkaline). Certain fibers are more resistant to each of these.
Gas Stream Moisture Level
Every bit as important as “gas stream chemistry” is understanding the amount of moisture in the gas stream, and the propensity to go through dew point during start up and shut down periods. This could not only have an effect on chemically activating the particulate, but also affect the ability of the filter properly being able to remove dust during pulsing (moisture will cause agglomeration of the particulate onto the bag causing a crust like surface that blocks air flow paths, and if severe enough, will require the use of treatments to the filter surface such as laminating with TTG ePTFE) to provide the best possible release characteristics.
3. Timely Cage Inspections
A thorough inspection of the cage is highly recommended each time new bags are installed. Some of the most frequent and common problems to look for when inspecting a cage include: bent and damaged wires, rusting and pitting, and sharp edges along the bottom of the cage pan.
4. Checking Pressure Drops (daily maintenance protocol)
Perhaps the most important indication of a dust collector’s performance is the differential pressure (resistance of air across the filters and clean air plenum). This measurement gives you an indication of whether your filters are operating correctly. Based on your system(s), the collector(s) should have been designed to operate within a set range of resistance, (measured in inches of water column). The differential pressure reading will indicate whether there is an issue with too low of a differential pressure (typically meaning the filters are allowing too much air to pass through which usually means emissions as well), or too high of a delta P (meaning flow is being restricted and will lead to reduced system flow capabilities and ultimately lower manufacturing capacity).
Our experts and field specialists recommend a proactive maintenance program where you are monitoring and trending how differential pressure is performing. In regards to critical process collectors, this should be done daily, and in regards to nuisance collection collectors – at least once a week. Upon seeing a negative trend, you can immediately start to evaluate potential problems with the process- are my cleaning systems operating properly? Are their leaks in the duct work causing outside air to be pulled in? Is material building up in the hopper causing erratic inlet flow distribution? Are my pick-up points balanced correctly to obtain the proper draft? Simply put, interpreting your pressure drop is like monitoring your blood pressure, and when done proactively, you can address potential problems before they cause serious plant production or emission issues
5. Check Cleaning Systems (daily/weekly maintenance protocol)
Ensuring your pulse jet dust collector cleaning system is operating properly is an imperative and proactive maintenance necessity. If you’re not getting proper cleaning due to a potential solenoid valve failure, diaphragm leakage or poor sealing, or perhaps inadequate supply (or recovery) of compressed air for pulsing, the desired performance of your system could be potentially compromised . In regards to critical process collector systems, these components should be checked at least weekly, and in some cases daily. Simply monitoring the entire pulse sequence and compressed air usage will help ensure problems are addressed immediately. When any of these parts are not operating properly, you are most likely dramatically reducing the effective cloth area (and subjecting filters being pulsed properly to take on an undesired flow of air and dust) of the system which can quickly affect productivity as pressure drops will rise and pick up points will lose designed draft.