What you didn’t know about baghouse start-up
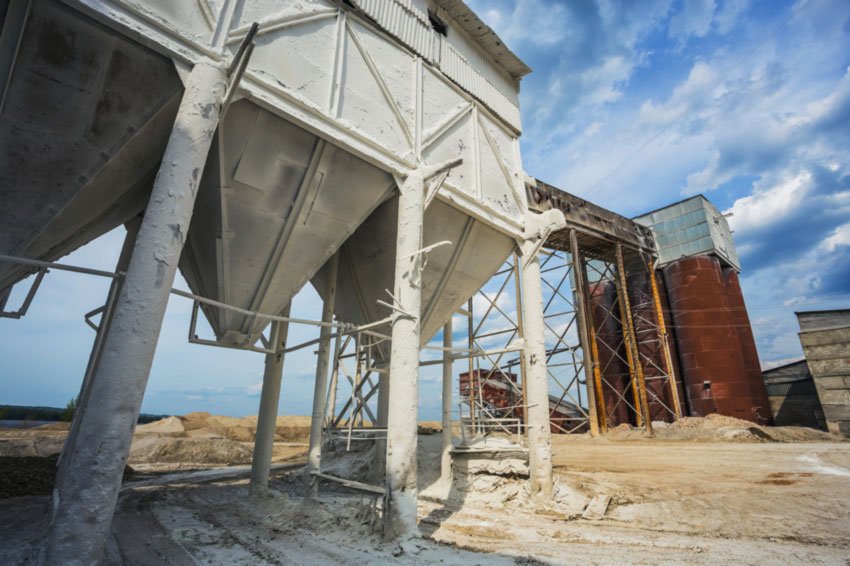
One of the core operations of IAC business is providing routine maintenance and inspection programs with the plants we work with. After many years of conducting inspections, repairs and start-ups we’ve noticed trends where the plants we work with are unaware of aspects involving maintenance. One particular issue that consistently arises involves pre-baghouse start-up inspections. Not only do we want to help our customers maintain their equipment, we want to educate them as well to avoid future issues.
IAC recently visited a plant to review and inspect the installation of the baghouses and related equipment in preparation for the upcoming startup. The following is a brief summary of the work performed and some recommendations to get the most out of your equipment.
Scope of Work
The request was to inspect 3 recently installed baghouses and test them for proper operation. The IAC Blue Crew checked for proper bag installation by reinstalling three bags in each unit and making sure all of the cages were properly seated on the tube sheet, which can indicate bag installation errors. Pulse pressure, controller settings and pulsing of all pulse valves were checked before checking the airlocks and activating fans to check for proper fan rotation. We also performed initial flow balancing to avoid over venting once the plant starts. Verification and secondary adjustment is recommended after the filter bags build up the recommended differential pressure.
General Recommendations
- Install compressed air regulators and adjust pulse pressure to approximately 80 psi. This applies for all IAC auxiliary baghouses. Compressed air is currently connected to the plant air system at 120 psi, which exceeds the recommended maximum for the pulse valves and will cause unnecessary wear on the filter bags.
- Program controllers with 160 millisecond pulse duration (on time) and time between pulses of 15 seconds (off time). This was done for the systems inspected.
- Program the controller to activate pulsing at the recommended high-levels (high pulse) and stop pulsing at a point slightly below that to maintain a uniform ΔP and avoid surges in discharged material. This was done for the three systems inspected.
- Because of extensive horizontal duct runs, we recommended non-restrictive duct inspection doors and periodically inspecting and cleaning buildup as required.
Other Observations
- Unnecessary openings on belt transfer enclosures need to be eliminated. De-dusting systems work by suctioning a draft of ambient air through necessary enclosure openings, avoiding dust emissions by sweeping fugitive dust. Large, unnecessary enclosure openings nullify capture velocity, reducing the effectiveness of the system.
- Adequate skirting at the enclosures need to be installed. Skirting is part of the enclosures, but was missing, leaving a much larger opening than necessary. As explained above, large openings nullify capture velocity and reduce
- Several vent hoods were positioned right next to the belt loading point, which cause some dust recirculation. Hoods work more efficiently when positioned farther away from the belt load point; closer to the end of the enclosure to reduce carryover.