Speed & Flexibility Ensure Successful Fast-Track Baghouse Replacement
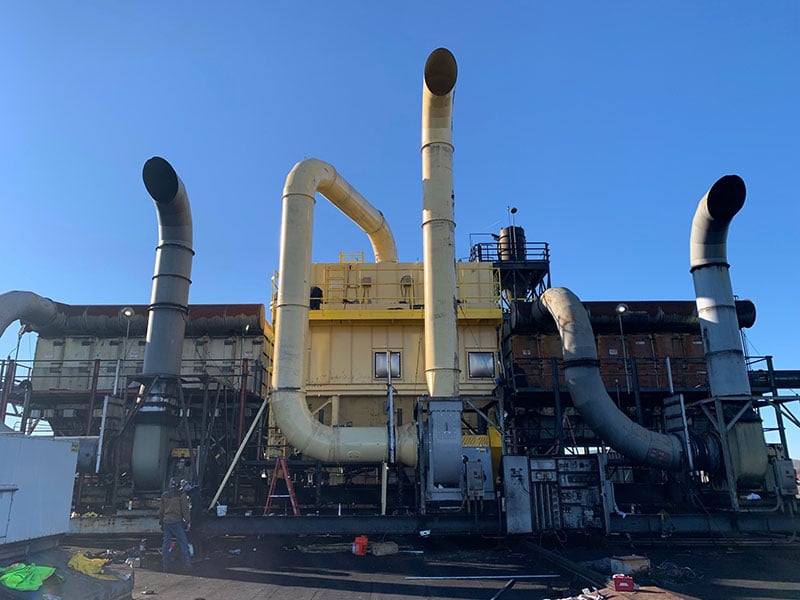
Baghouse dust collectors are critical process equipment for many manufacturers, so when one reaches the end of its serviceable life, replacing it before it goes down can prevent loss of valuable production time.
At the beginning of September 2021, one of IAC’s customers in the tire manufacturing industry contacted us because they’d been having issues with one of their main process baghouse dust collectors. The baghouse was used to vent and reclaim very fine carbon black particles during the mixing process.
The unit was an older, roof mounted, baghouse that had been requiring constant shutdown maintenance for leak testing. The original baghouse design utilized envelope style filters which don't seal well. Over time, corroded blow pipes, cracks in welds, and pin holes in side walls were costing the customer too much money due to maintenance downtime chasing leaks. Additionally, its caulking and flanges had worn out, and the interior had been coated with spay foam in an attempt to keep it sealed and functioning.
IAC's Inside Sales and Field Maintenance teams performed a site visit and worked with the customer to implement short-term fixes, but the baghouse had clearly reached the end of its serviceable life.
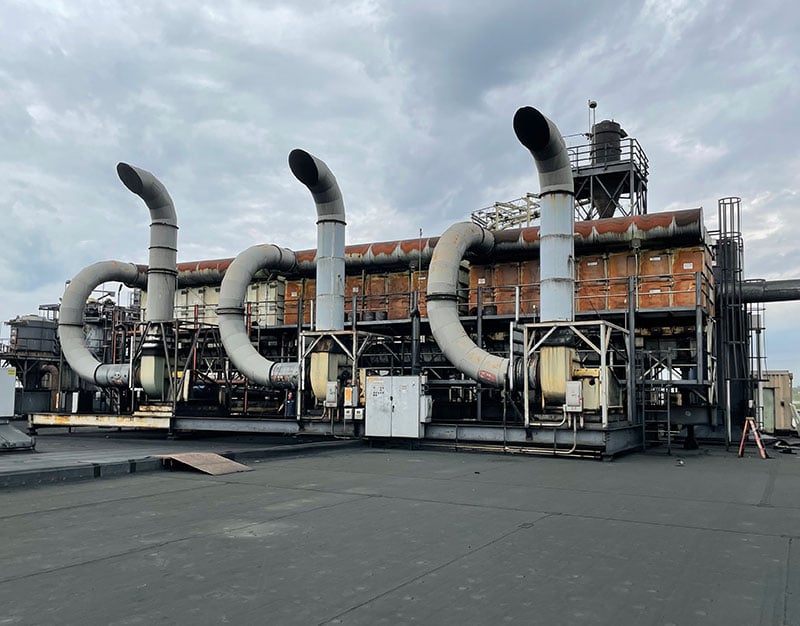
Located on a rooftop, the center baghouse dust collector had reached the end of its serviceable life.
The customer commissioned IAC to perform an engineering study and write a design spec for a new 30,000 cfm Pulse Jet baghouse with a walk-in plenum, plus all the ductwork to connect the baghouse to the plant. Having a baghouse company such as IAC write the report and spec was important because our professional engineers (PE) write in unbiased “baghouse speak”, understandable by any baghouse manufacturer, which accelerated the bidding process.
After receiving our PE’s report, the customer sent it out for bid with a requirement that the project needed to be completed by the end 2021. During ‘normal’ years this tight of a turnaround would be difficult, but during the 4th quarter of a year of material shortages and extended lead times, the customer was asking for the near impossible. None of our competitors could guarantee meeting the customer’s fast-track project schedule.
IAC was able to accept the customer’s purchase order on September 14th, and within 14 weeks, have the new baghouse, plus ancillary equipment and ductwork, installed. This included finalizing the engineering prints, manufacturing or procuring all the necessary components, transporting equipment to the jobsite, then executing the demolition of the old baghouse AND installation of the new baghouse in just five (5) days to minimize production downtime.
IAC's OEM metal fabrication & logistics teams coordinated production and delivery to the job site.
Throughout the fourteen weeks, IAC’s project manager took good news and setbacks in stride. He always worked in a forthcoming manner with internal teams and outside vendors to ensure the project kept moving forward.
The week before Christmas, despite adverse weather conditions including three days of rain and a thunderstorm that shut down the jobsite for several hours, the Adelphi crew persevered. A 500-ton crane was used to carefully lift the old baghouse off the roof and lower it to the ground. The fan and ductwork were also removed.
Removing the old baghouse dust collector at night with a 500 ton crane required precision handling.
Next, the crew began to install the new modular Pulse Jet baghouse. With only a narrow allowance of 3” of clearance on each side, the crane operator had to perform a precision pick from the ground, lift the new baghouse unit over multiple objects, then lower it down onto the rooftop into its location between two other baghouse units. Once the baghouse was in place, the Adelphi crew focused on installing the high efficiency centrifugal fan, ductwork, and electronic controls.
Finally, the pleated filters were installed and a leak test was conducted to ensure the filters and baghouse were properly sealed. A screw conveyor was connected to the existing port, and the new baghouse dust collector went online December 22nd, 2021.
The plant manager and the plant engineering manager stated they were very pleased with IAC’s baghouse design and performance, and also with the IAC and Adelphi installation crews. They’ll be contacting IAC again for future baghouse installations.
Adelphi Construction crew members finish installing the new 30,000 cfm Pulse Jet baghouse.
When time was of the essence, IAC's dedication to fast-track construction and project management practices, control over production costs and schedules, and robust supply and logistics chains kept our customer's production line running smoothly.
Contact us today and let our team help keep your plant's production!