Glossary of Rotary Dryer Terms
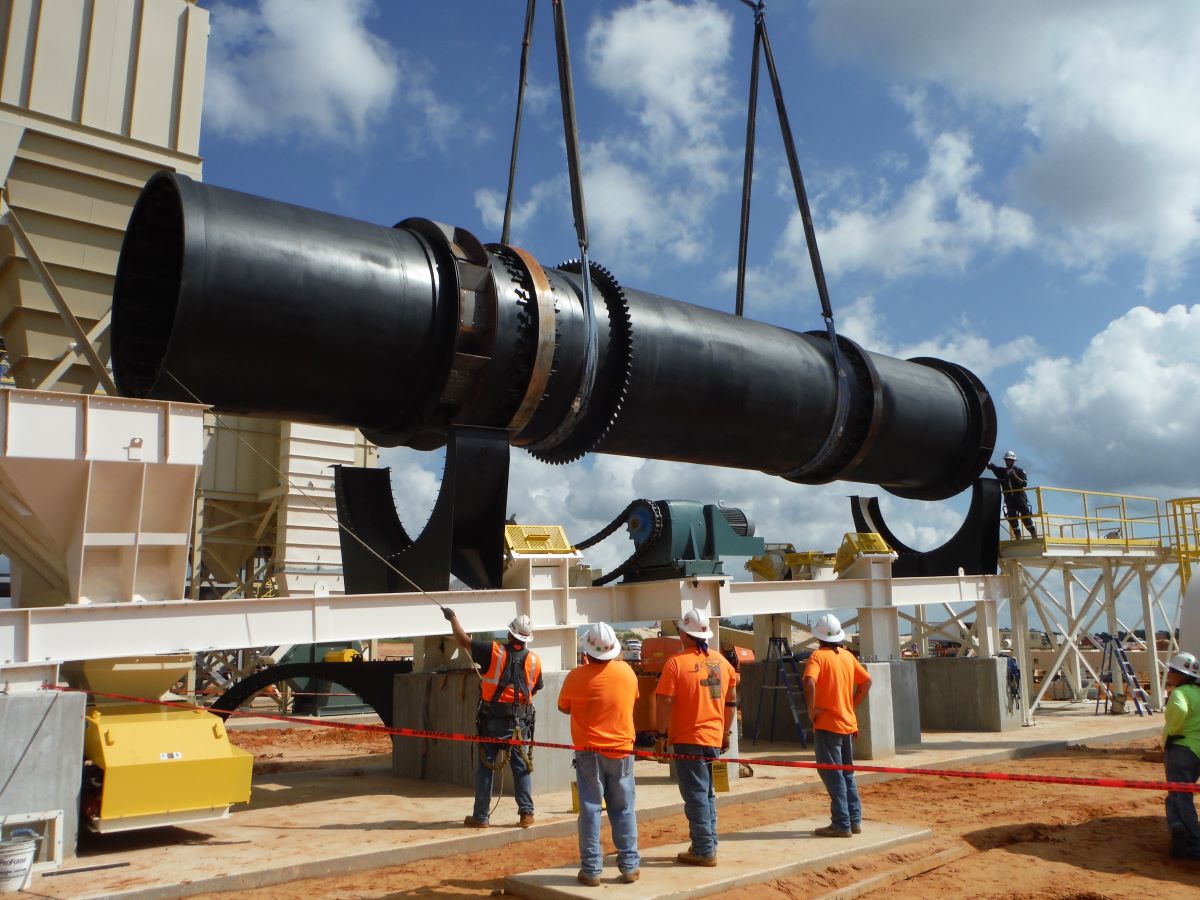
Rotary dryers play a pivotal role in various industrial sectors, providing a highly efficient and cost-effective solution for drying bulk materials. The intricate design of these industrial rotary dryers enables them to handle a wide range of materials, including aggregates, biomass, minerals, and waste products. This advanced technology has revolutionized the drying process, ensuring optimal performance, versatility, and reliability. Delve into this comprehensive glossary to gain insights into the cutting-edge engineering and innovative developments shaping the future of rotary dryers, and explore their potential to transform your business operations.
Rotary Dryers Defined
Rotary dryers are cutting-edge industrial drying systems designed to efficiently remove moisture from bulk materials. These advanced dryers utilize a cylindrical drum and intricate heat transfer mechanisms for exceptional drying performance. The drum, the central component of the dryer, rotates slowly, allowing the material to cascade through the hot gas stream. This gentle cascading action maximizes the material's exposure to the heated surface, facilitating rapid and uniform moisture evaporation.
What sets rotary dryers apart is their versatility and adaptability to diverse applications. Industry experts appreciate the precise control these dryers offer, as they can be customized with variable speed drives, adjustable flights, and innovative sealing mechanisms to optimize drying efficiency. Additionally, rotary dryers are designed with advanced features such as heat recovery systems, cyclones, and bag filters to minimize energy consumption and ensure environmentally friendly operation. The intricate interplay between heat, airflow, and material dynamics within rotary dryers results in impressive drying capabilities, making them a key asset in various industries.
Types of Rotary Dryers
Direct Heated Rotary Dryers
Direct-heated rotary dryers are used when products are not sensitive to high temperatures. These dryers have rotary drums in direct contact with hot air or combustion gases, providing efficient heat transfer and quick evaporation. This results in reduced drying times, making them suitable for a wide range of industrial applications where large quantities of materials need to be dried quickly.
Indirect Heated Rotary Dryers
Indirect heated rotary dryers are employed when materials require gentle handling, and exposure to high temperatures can cause damage. These dryers heat the rotary drum indirectly using steam, hot water, or thermal oil, thus avoiding direct contact between the heat source and the material. The indirect heating method reduces the potential for product degradation and is ideal for drying temperature-sensitive substances or products that can combust in heat.
Vacuum Rotary Dryers
Vacuum rotary dryers operate under reduced pressure, lowering water's boiling point and enabling evaporation at lower temperatures than atmospheric conditions. These dryers are particularly suitable for heat-sensitive materials, delicate products, or those that could pose a safety risk if exposed to high temperatures. In addition, vacuum drying minimizes the risk of product contamination, making it ideal for applications that require a high level of cleanliness.
Rotary Cascade Dryers
Rotary cascade dryers use a rotating drum and specially designed lifters to lift, cascade, and tumble the material through the hot gas stream. This process maximizes heat transfer and promotes efficient drying of the material. The continuous cascading action produces a uniform product with minimal temperature variations, making these dryers suitable for various industries, including minerals, chemicals, and food processing.
Rotary Cone Dryers
Rotary cone dryers are designed with a conical-shaped drum that helps to promote efficient mixing and drying of the material while ensuring easy discharge. These dryers offer uniform drying, low energy consumption, and are suitable for materials requiring gentle handling or varying particle sizes. Rotary cone dryers are commonly employed in the pharmaceutical, chemical, and food industries.
Fluid Bed Rotary Dryers
Fluid bed rotary dryers combine the benefits of fluidization and rotary motion drying for efficient heat transfer and gentle handling of materials. These dryers use hot air to lift and agitate the product, allowing moisture to evaporate quickly and uniformly. Fluid bed rotary dryers are ideal for fine powders, granules, and crystals in chemical, pharmaceutical, and food processing industries.
IAC Engineers, Manufacturers, Installs, & Maintains Industrial Rotary Drying Systems! Watch our Industrial Drying Systems video to learn more!
Benefits of Rotary Dryers
High Efficiency and Large Capacity
Industrial rotary dryers are known for their high efficiency in drying large quantities of materials relatively quickly. It is due to their unique design that promotes uniform heat transfer and efficient use of thermal energy. As a result, businesses can achieve higher throughput, reduce energy consumption, and save on operational costs.
Versatility in Drying Applications
Rotary dryers are designed to accommodate a wide range of materials, making them versatile solutions for various industries. They can handle various feedstock, including liquids, sludges, and solids, making them ideal for mineral processing, chemicals, food, and agricultural products. With their robust design and adaptability, rotary dryers can easily be adjusted to achieve optimal drying conditions for different materials.
Consistent Product Quality
One of the key advantages of industrial rotary dryers is the ability to deliver consistent product quality. Their precision in controlling temperature, residence time, and moisture levels enables businesses to maintain optimal drying conditions throughout the drying process. This ensures that the final product meets desired specifications, minimizes product degradation risk, and increases overall product quality.
Components of Industrial
Rotary Dryers
Industrial rotary dryers are sophisticated machines designed to efficiently dry bulk materials. They comprise advanced components that work in synergy to achieve optimal drying performance. Understanding the intricate details of these components is crucial for maximizing efficiency, ensuring reliable operation, and meeting specific drying requirements. Let us know the components of industrial rotary dryers and their key functions in drying.
Shell
The shell serves as the primary structure of the rotary dryer and is typically constructed from durable materials such as stainless steel or carbon steel. It is designed to withstand high temperatures, pressure differentials, and the mechanical stresses associated with rotation. Advanced rotary dryer designs may incorporate double or triple shells with insulation layers to enhance thermal efficiency and reduce heat loss.
Flights
Flights, also known as lifters or paddles, are integral components attached to the interior of the dryer shell. Their primary role is to lift and cascade the material as the dryer rotates, facilitating efficient heat transfer and ensuring uniform drying. Advanced flight designs consider factors such as flight angle, configuration, and spacing to optimize drying performance for specific materials, ensuring adequate residence time and minimizing material accumulation or buildup.
Burner
The burner is a critical component responsible for generating the heat required for drying. It combusts various fuel sources, including natural gas, propane, or waste gases, to produce a high-temperature flame or hot gas stream. Advanced burner systems may incorporate technologies like modulating burners or multi-fuel capabilities, allowing precise control over heat output and enhancing energy efficiency.
Air System
The air system is a complex network of fans, blowers, and ductwork that facilitates the controlled air flow through the drying chamber. It plays a vital role in maintaining the desired airflow patterns, temperature control, and moisture removal. Advanced air system designs include variable frequency drives (VFDs) for precise airflow modulation, heat recovery systems for improved energy efficiency, and advanced air distribution mechanisms for uniform drying across the material bed.
Drive System
The drive system provides the rotary motion necessary for the dryer's operation. It typically consists of an electric motor, gear reducers, and drive chains or belts. Advanced drive systems employ sophisticated control mechanisms to ensure precise speed control, torque management, and reliable operation. They may incorporate advanced sensor technologies, such as encoders, to monitor and optimize the rotational speed and ensure consistent material residence time.
Control System
Modern industrial rotary dryers feature advanced control systems that monitor and regulate various parameters critical to the drying process. These systems may include programmable logic controllers (PLCs), human-machine interfaces (HMIs), and sophisticated algorithms for precise temperature control, moisture sensing, process optimization, and safety monitoring. Integration with supervisory control and data acquisition (SCADA) systems enables remote monitoring, data logging, and advanced process analysis.
Working Principles of Rotary Dryers
Rotary dryers are advanced industrial drying systems that utilize the principle of indirect heat transfer to efficiently remove moisture from various materials. The working principles of rotary dryers involve a complex process that ensures effective and reliable drying performance.
In a rotary dryer, the material to be dried is fed into a rotating cylinder or drum, which is typically inclined slightly to facilitate the movement of the material. As the drum rotates, it is heated by a direct or indirect heat source. The heat source can be combustion gases, hot air, or steam.
The dried material is lifted by specially designed internal flights or lifters within the drum, which promotes intimate contact between the material and the heated surfaces. This contact facilitates heat transfer from the drum to the material, causing the moisture within the material to evaporate. The evaporated moisture is then carried away by the drying medium, which can be air or other gases.
The rotating action of the drum ensures that the material is constantly exposed to fresh surfaces, maximizing the drying efficiency. The movement of the material through the drum is influenced by factors such as the drum's rotation speed, angle of inclination, and design of the lifters.
The exhaust gases or drying medium are directed out of the drum through an exhaust system, while the dried material is discharged from the opposite end of the drum. Internal or external mechanisms, such as flights or screw conveyors, can facilitate discharge.
Applications for Rotary Dryers
Chemical Industry
- Used for drying various types of granulated and crystallized chemicals like salts, pigments, and fertilizers to improve product quality and reduce transportation costs.
- Helps maintain a controlled environment during the drying process, minimizing the risk of chemical reactions and ensuring product safety.
- Efficient removal of moisture from feedstock, improving the overall efficiency of chemical processes, and reducing energy consumption.
Pharmaceutical Industry
- Drying of bulk pharmaceutical powders and granules to ensure proper moisture content, improving product stability and shelf life.
- Continuous rotary dryers provide uniform and consistent drying, maintaining product quality and preventing clumping or caking of powders.
- Suitable for drying heat-sensitive materials, as they allow for precise temperature control and indirect heating.
Food and Agriculture Industry
- Used in the drying of various agricultural products, such as grains, seeds, and animal feed, ensuring the safe storage and transportation of these products.
- Minimizes the risk of spoilage and mold growth by effectively reducing moisture content in food products.
- Enhances the shelf life and preserves the nutritional value of dehydrated fruits, vegetables, and spices.
Mineral Processing Industry
- Used for drying mineral ores, concentrates, and tailings, facilitating their further processing and transportation.
- Effectively removes bound moisture from fine and coarse materials, allowing for easier handling and storage.
- Can be efficiently integrated into larger processing plants, reducing overall operational costs and increasing equipment lifespan.
Waste Management and Recycling Industry
- Used in the drying of municipal and industrial sludge, reducing the volume and weight of waste for disposal or reuse.
- Can be used to process and dry a wide variety of materials, including paper, plastics, and metals, for recycling purposes.
- Helps meet stringent environmental regulations by reducing the moisture content of waste materials before disposal, minimizing the risk of groundwater contamination.
Frequently Asked Questions About Industrial Rotary Dryers
1. What are some emerging technologies and innovations in industrial rotary drying?
Several emerging technologies and innovations are revolutionizing the drying process in industrial rotary drying. Advanced control systems with predictive algorithms and real-time monitoring optimize energy utilization and improve product consistency. Heat recovery systems, such as air-to-air heat exchangers, recycle waste heat, enhancing energy efficiency. Innovative airflow patterns and drying techniques, like counter-current and cross-flow drying, enhance drying uniformity and reduce drying time. Novel drum designs with optimized flight geometry and heat transfer surfaces improve drying efficiency. Integration of IoT and Industry 4.0 enables data-driven optimization and predictive maintenance. These advancements enhance drying performance, energy savings, and improved product quality.
2. Are there any regulatory or compliance considerations when using a rotary dryer in an industrial process?
When using a rotary dryer in an industrial process, there are regulatory and compliance considerations that industry experts should be aware of. Specific environmental regulations and emission limits may apply depending on the region and industry. Compliance with air quality standards and emission control measures, such as air pollution control equipment, may be required. Additionally, occupational health and safety regulations must be followed to ensure a safe working environment for operators. Proper permits, licenses, and documentation may be necessary to demonstrate compliance with applicable regulations. Industry experts must stay updated with relevant regulations and engage with environmental and regulatory authorities to ensure compliance and maintain sustainable operations.
3. What are the maintenance requirements for industrial rotary dryers?
Maintenance requirements for industrial rotary dryers are crucial to ensure optimal performance and longevity. Industry experts should prioritize regular inspections, cleaning, and lubricating key components such as trunnions, bearings, gears, and seals. Monitoring and adjusting the dryer's alignment, belt tension, and burner operation is vital for efficient drying and preventing mechanical issues. Scheduled preventive maintenance activities should include checking and replacing worn or damaged parts, inspecting electrical systems, and cleaning dust collection systems. Implementing condition-based maintenance strategies, such as vibration analysis and thermal imaging, can detect early signs of equipment degradation. By adhering to a comprehensive maintenance plan, industry experts can maximize industrial rotary dryers' reliability, efficiency, and lifespan.
IAC engineers, manufactures, installs, and maintains industrial rotary dryers, including burner design and control.
Contact us today for all your industrial drying needs!