IAC Baghouse Installation Eliminates Harmful Powder Exposure
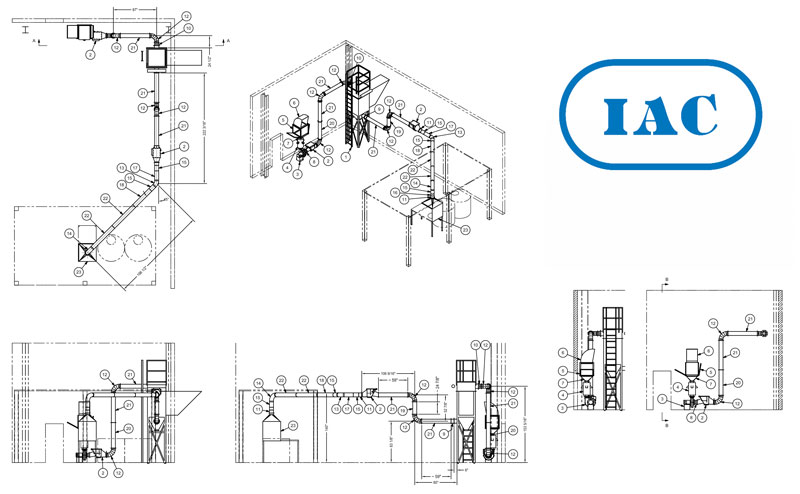
Many of IAC’s customers work with dangerous and hazardous materials. When creating solutions for handling harmful materials, IAC works quickly to help these organizations create safer processes for their employees and production. IAC did this recently by taking a few fast measurements and rapidly creating a custom component to eliminate the spread of a harmful powder in an ingredient facility, which took numbers from three and a half times the exposure limitation to less than 10% of the threshold.
“We expedited the engineering drawings and the fabrication for this project due to the fact that it was a health and safety concern for the employees involved,” IAC Aftermarket Equipment Sales Manager Tony Pray said.
The facility’s production manager said the issue occurred in an area where large bags of powder are cut open, dumped into a small hopper, and mixed with water. Once mixed with water, the ingredient becomes a binding agent.
“It created so much dust that anyone in the area had to wear a respirator,” Pray said. “As it covered the floor, if it became wet, it would make the floor sticky and hazardous to walk on. So, there was housekeeping happening on every shift. The whole area had to be hosed off.”
The facility carried out an Industrial Hygiene (IH) test and the production manager said the results exceeded the normal limit. They had to act quickly to keep employees from breathing the dust and to make the workplace cleaner. They began looking at dust collection options and felt IAC offered a more turnkey solution because the facility could receive a complete package to have installed.
“One other challenge is, we have a lot of dust collection equipment in plant, but don’t deal with explosive dust at all really,” the production manager said. “The guys I worked with [at IAC] made sure to put the right explosion protection in place and help mitigate the risk.”
To ensure all equipment met the needs of the facility and eliminated the need for repeated housekeeping every shift, IAC installed a small pulse-jet top load dust collector with pleated bags. The order also included a custom hood, explosion panels, and a HEPA filter on the back of the fan to return clean air into the facility.
“The numbers we were getting when we started the (IH) sampling were about three and a half times the upper limit that we wanted to expose anybody to,” the Production Manager said. “Once we finished [installing the dust collector] they were less than 10% of the allowable the limit.”
The facility’s production manager said the area is now clean and the company can contain the dust properly. Employees began working without respiratory protection in less than a week of the installation. Follow up testing at the facility has continued to show low results. Employee feedback has been overly positive.
“There’s been a lot of good feedback from the people that do this job that they could tell once we put this equipment in, they felt a lot cleaner,” said the Production Manager. “We got a lot of good comments about how much better the work environment was.”
This successful change within the environment has spurred the customer to address a similar situation in their packaging area. While the dust there is not dangerous, packaging the powder has led to excessive housekeeping. IAC will soon install a similar dust collector in this area to minimize housekeeping and maximize production.
Find out how IAC can help evaluate and remediate hazardous powder and dust in your industrial plant or mining facility!