Introduction to Acoustic Cleaning with Sonic Horns
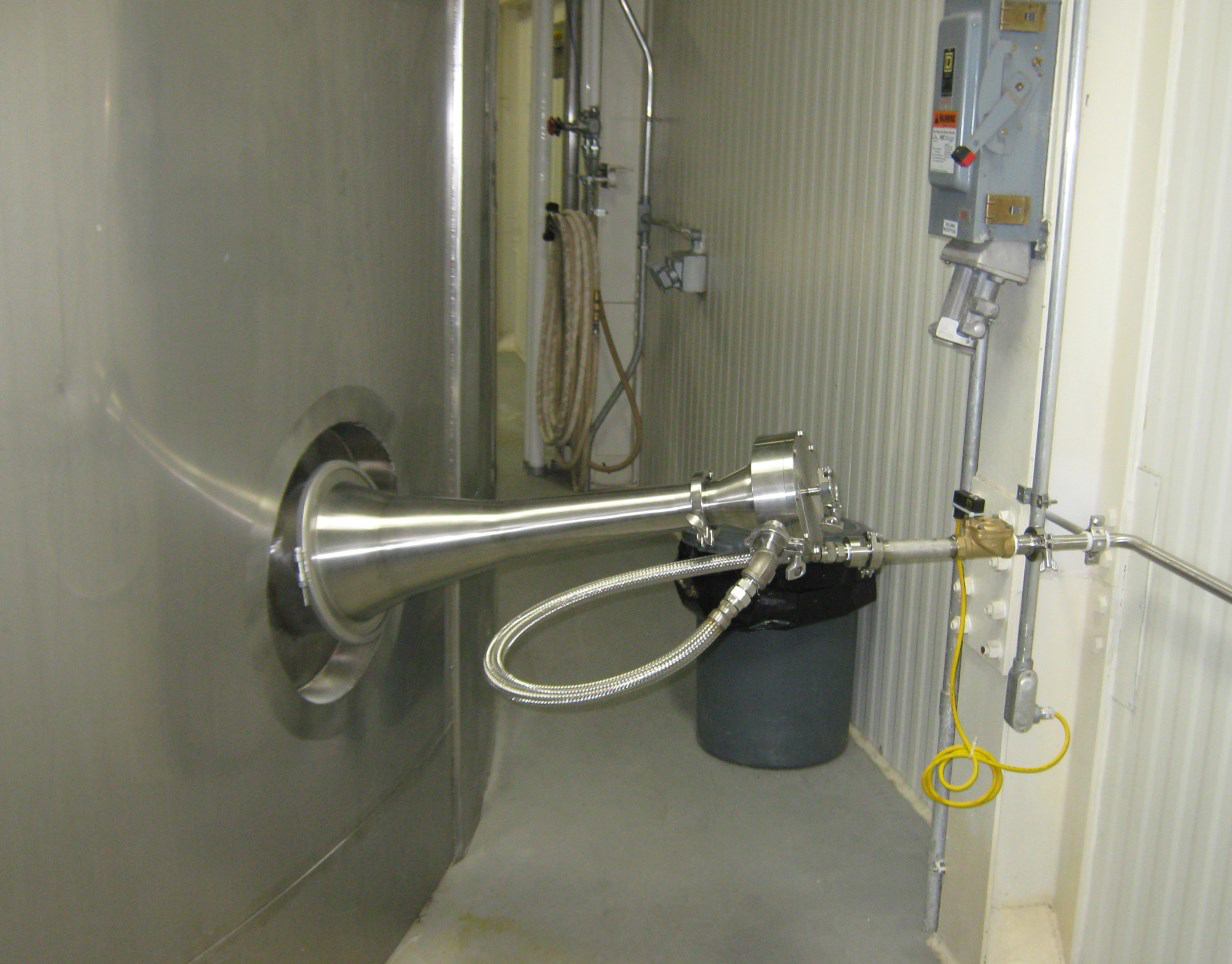
Sonic Horn Acoustic Cleaning History
The use of sound vibrations produced by sonic horns, as a means of fluidizing unwanted dust and agglomerated particulate in industrial process equipment, has been a well accepted practice for years. Sonic horns have been used to clean filter bags in baghouses in the carbon black and cement industries since the 1950s. These early sonic horns proved that acoustic energy could improve filter bag cleaning in conjunction with the primary reverse-air cleaning however their benefit was not fully realized throughout the industry as they are today.
Sonic horns began their present popularity in the 1980’s after the utility industry started using sonic horns to help reduce baghouse pressure drop, which was limiting plant generating capacity. Sonic horns became extremely cost effective in improving bag cleaning, thus increasing the power plants megawatt generating capacity.
|
![]() |
600 MW Coal Fired Boiler Utility Baghouse |
Sound Level and Fundamental Frequency for Sonic Horn Cleaning
Each manufacturer’s sonic horns are different in design, size and shape, which are all factors that affect their sound level and fundamental frequency. The sound level and the fundamental frequency are the two main characteristics of the sonic horn’s acoustic energy. This acoustic energy consists of a sound with multiple frequencies. The most effective sonic horns produce the majority of its sound at its fundamental frequency. However many sonic horns cannot accomplish this and produce more noise than vibrations, which make them less effective in sonic cleaning.
IAC Sonic Horns are specifically designed to produce and amplify low frequency sound vibrations at a high intensity for effective removal of unwanted particulate build-up.
Optimal Acoustic Energy and Frequency for Sonic Cleaning
Acoustic energy at a frequency range of 63 to 250 Hz (Hertz - cycles per second) have proven to be the optimum frequencies for sonic cleaning. Frequencies above 300 Hz are less effective in sonic cleaning and are more audible and annoying to the human hearing. These low frequencies have higher reflectivity of solid surfaces, resulting in less absorption of sound. Low frequencies are also more omni-directional and result in more uniform penetration of sound throughout an enclosed area. Whereas, higher frequencies above 300 Hz are more directional and they dissipate at a faster rate. This does not necessarily mean that the lower the frequency the better. There is a point at which acoustic energy can become destructive to
solid structures and mechanical connections. This occurs in the frequency range below 60 Hz.
The other important acoustic characteristic of the acoustic energy is the intensity or sound pressure level (SPL). The sound pressure level is usually measured in decibels (dB). The intensity of the fundamental cleaning frequency, which fluidizes the particulate build-up must be above 120 dB. The greater the intensity or SPL, the more effective the cleaning. Sound pressure level measured in decibels can be misleading when comparing power or energy levels, because decibels are a non-linear measurement. The difference between 130 dB to 140 dB may seem insignificant, but it actually corresponds to a factor of 10 difference in the power available. And a change from 120 dB to 140 dB is only a 17% increase in dB level, but a hundred-fold increase in power. High-pressure pulses of compressed air create the acoustic energy produced by the sonic horn. The acoustic energy is produced by applying 60 to 80 psi of compressed air to the sonic horn’s driver, which vibrates a high-strength diaphragm contained inside. This acoustic energy has a fixed frequency band determined by the shape and size of the horn’s bell. |
![]()
|
IAC Sonic Horn Sound Intensity
IAC Sonic Horns produce sound intensities of 140 dB+ with fundamental frequencies ranging from 63 to 160 Hertz. This rating is measured at one meter from the bell mouth in free air. “Free air” means no amplification of the sound pressure level due to reflective surfaces. The dB level or intensity of the sonic horn’s free air output can increase from 3 to 6 dB when sounded in a enclosure with solid reflective surfaces.
Sonic Horn Models
IAC offers six standard Sonic Horns with ability for customization in material and mounting, including stainless steel with sanitary finish for USDA applications. View models and technical specifications on our sonic horn product page. You can also view or download our Sonic Horn Catalog (PDF).
Sonic Horn Installation and Maintenance
Information on how to install and maintain a sonic horn can be found on our How to Install and Maintain a Sonic Horn page.
Our parts and engineering experts are available to answer your questions about Sonic Horns and acoustic cleaning to remove material build-up in dry bulk handling, conveying, and storage systems. Reach out and connect with us by chat, telephone, or submit our simple request for quote form.