Fresh Lungs for Pneumatic Conveying Systems
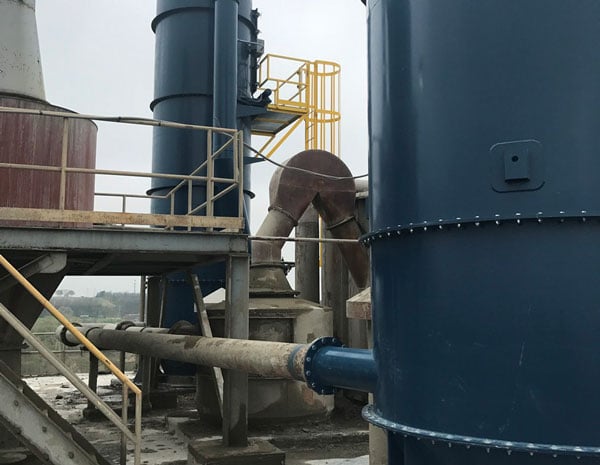
A cement plant in the northeast has multiple pneumatic conveying systems, each capable of transporting 100 tons per hour of cement from the plant to their bulk loadout silos. These pneumatic transport systems use powerful compressors to push product through conveying pipes hundreds of feet away, and 170’ up to the top of the silos.
At the receiving end of each of these conveying systems, the original designers considered a cyclone for partial product removal, followed by a conventional baghouse to remove cement from the conveying air before releasing it to atmosphere. The cyclone did not have a discharge airlock device, and the baghouses had extensive housing cracks, from decades of positive to negative pressure cycles.
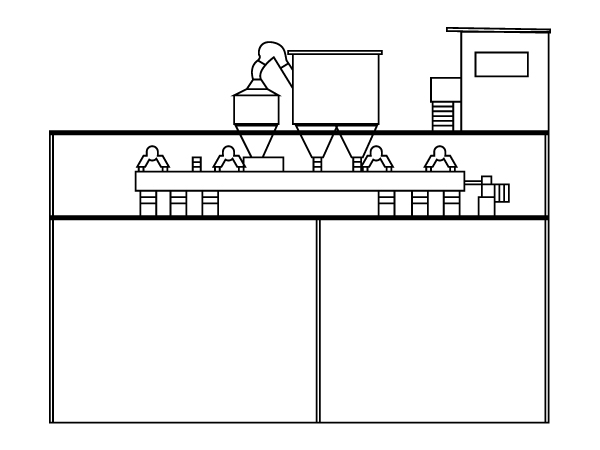
Problem
Even with the systems operating adequately, the plant learned to live with a thick cloud of cement dust in the silo penthouse, mainly due to pressurization of the screw conveyor. This not only caused severe housekeeping problems and poor working conditions, but also resulted in cement contamination as a result of continuous buildup problems and manual cleanup and recovery inside the penthouse.
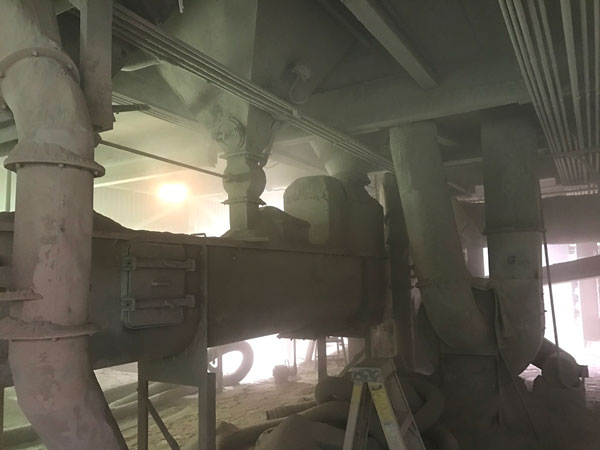
Requested Solution
To fix these problems, the plant asked suppliers to bid new baghouses, leaving the rest of the system untouched. Several bidders diligently submitted their proposals to replace these baghouses, while IAC engineers decided to analyze the situation in more detail.
Real Solution
Being a solutions provider and not just an equipment supplier, IAC reviewed the existing installation and suggested the correct solution: To install a modern IAC Filter/Receiver (F/R) for each system.
Filter Receivers look like pulse jet baghouses, but are made for high grain-loading, high-pressure pneumatic conveying system applications. Each F/R has an integrated cyclone for efficient product separation, a cylindrical housing that supports pressure cycles without fatigue, high efficiency PTFE membrane filter bags, and a single airlock discharge point to deliver cement to the distribution screw conveyor – free of pressurization.
IAC’s elegant solution was chosen and implemented, providing reliable, efficient and dust-free product conveying to the finish silos, something dreamed of in 1959, but finally accomplished in 2017.
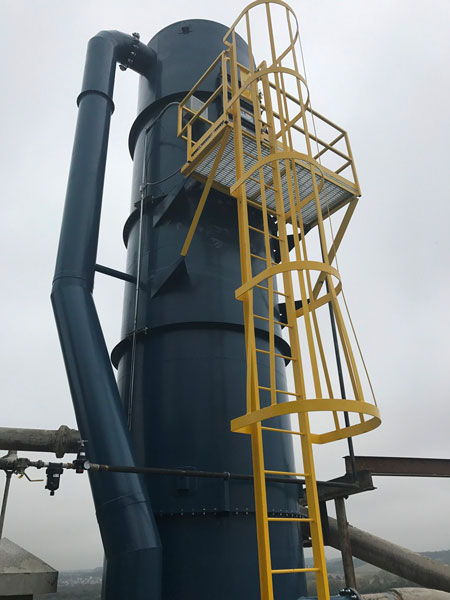
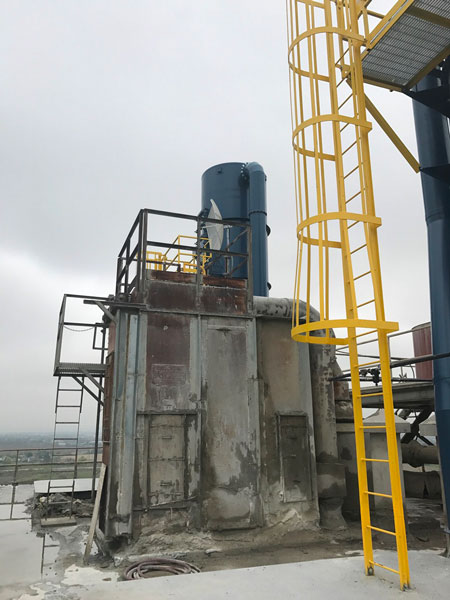