Predictive Maintenance Solutions for the Steel & Iron Industry
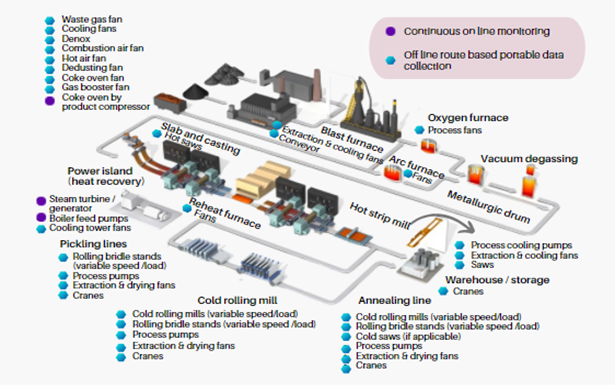
Unreliable assets have enormous consequences. What if your assets could consistently operate at or above their rated capacities, for a greater percentage of total hours each year, all while spending less money on maintenance?
That’s exactly what today’s best companies have discovered how to do. Industry studies show that the average facility spends approximately 5% of its Replacement Asset Value (RAV) on maintenance each year. In comparison, best performers spend 60% less—just 2% of RAV—while enjoying better uptime, efficiency, and profitability. It’s not about simply spending less on maintenance; it’s about working differently—working smarter—to achieve more reliable steel production operations.
Steel and Iron Manufacturing Industry Challenges
Equipment Reliability: The Key to a Successful Future
- Currently the steel industry envisages more than 300 million tones (MT) steel-making capacity which will gradually be 160 kgs per capita steel-consumption by 2030-31.
- Steel making processes are highly energy-intensive and comprised of many complex unit operations.
- Steel is more or less utilized in every industry.
- Equipment in steel manufacturing plant operates 24 X 7 for maximum productivity.
- Improper handling of bearings and its lubrication affects the sintering process. Inspecting vibrations on the equipment can safeguard operational performance.
- Preventing the time-consuming dismantling process of gear assembly by monitoring it, facilitates operations of the conveyor belts and Blast Oxygen Furnace.
- Tracking the harmonics of the bearings of low-speed overloaded casting machines enhances the transportation of semi-furnished products.
“60% of the equipment defects are predicted by vibration analysis and 85% of the predicted defects can be prevented by remedial actions to reduce the equipment downtime and avoid the production loss”.
![]() |
SMART Rotary™
|
When implementing a new predictive maintenance program, here are three areas you must address:
Processes: IAC can help customers assess their goals, identify the reliability gaps in their current operations, and then implement the appropriate corrective actions and strategies to keep operations running smoothly.
Tools: Everything needed to address the assets in automotive plants and other metal production facilities are available, from sensors to continuous monitoring systems to wireless sensor systems to portable data collectors and analyzers. And it’s all brought together in a unified platform for predictive asset maintenance - SMART Rotary™ software. We also assist customers in integrating and using their already installed tools, such as computerized maintenance management systems (CMMS) and reliability software.
People: Reliability is about more than just technologies and processes. Armed with even the most sophisticated tools and effective strategies, companies can only reach their reliability goals if they can change how they work successfully. Reliability is a company-wide effort that touches operations, maintenance, planning and scheduling, purchasing, management, and engineering. IAC can help customers change how they work by addressing the organizational culture issues that keep companies mired in ineffective processes, helping them transform their businesses and balance sheets.
IAC provides SMART Rotary™, a turnkey, universal and autonomous predictive maintenance solution for industrial equipment.
Designed for anomaly detection based on machine learning, IAC has created a universal solution to monitor machines of different ages and designs, without constraints of installation and deployment.
This scalable and flexible technology maximizes your machine performance while lowering operational and maintenance costs by providing your teams with sophisticated data collection technologies and real time analytics to help them monitor and manage your KPIs.
Remote Monitoring Solutions that are Simple Plug & Play
- Simple to install. Just place it on your machine. No wiring nor configuration is required.
- Secure by design - designed for harsh or even explosive environments
- Extensible to Cloud-based dashboards and usage reporting, additional custom alarms, or integration to 3rd party applications.
- Connected to a scalable and resilient environment.
- Autonomous - Work for several months without recharging (battery included).
With IAC's extensive portfolio of Smart Plant™ Remote Monitoring products and services, you can meet steel and iron manufacturing industry challenges.
Predictive Maintenance Sensors Designed to Suit Every Need
SMART Rotary™ monitors and analyses any rotating machine and helps to predict anomalies, wirelessly and non-intrusively, with a simple installation. Sensors communicate through a LoRa (long range network) and data is encrypted end-to-end. IAC’s sensors monitor not only heat and vibration, but ultrasound too, meaning customers have the earliest possible alert of drift - before any damage has occurred.
- Vibrations: Looseness, imbalance, misalignment, advanced degradation.
- Ultrasounds: Lubrication issues, early signs of rolling degradation, gas leaks.
Data is processed at the edge on the sensors and then the information is transferred and stored in the cloud through an encrypted secure network and then accessible through web applications.
Visualization + Analytics + Prediction = A Complete solution
Generate significant savings annually!
SMART Rotary™ machine predictive maintenance solutions combine advanced hardware, intelligent software and trusted service and support – providing a broader, connected view of your operations. These solutions enable steel and iron operations to mitigate operational risk, enhance the safety of operations, and reduce maintenance costs.
By implementing these solutions, actionable insights based on asset health can be developed to optimize outage and maintenance planning. This can result in a 5-10x cost reduction compared with unplanned and reactive outages. SMART Rotary™ also offers cybersecurity solutions to ensure that steel and iron plant systems are up-to-date and protected from continually evolving threats.
Typical integrated steel manufacturing plant process
The implementation of industrial data enabler in steel plants, especially to monitor:
- Process of smelting and sintering.
- Split bearings on the conveyor belts.
- Tapered roller bearings in continuous casting machines.
- Gear boxes in the blast oxygen furnace.
...can turn more of the critical unknowns into knowns!
Monitoring equipment used in steel plant