The Importance of Baghouse Insulation
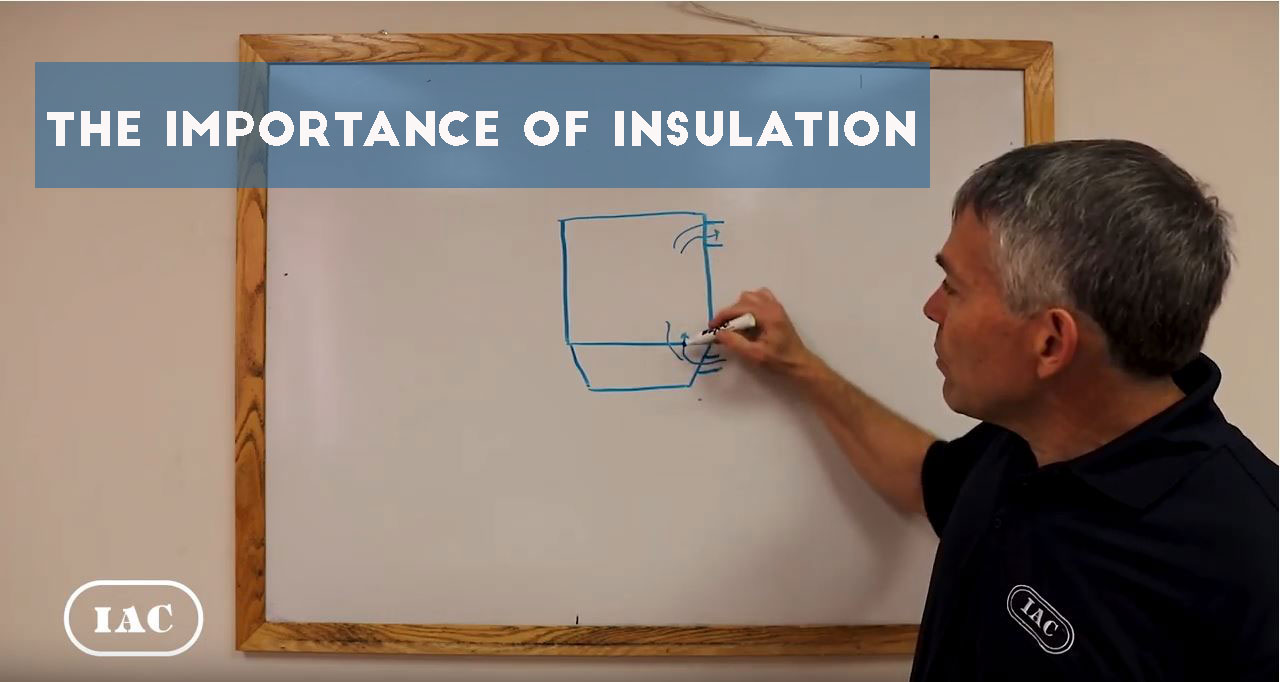
Insulation is an important aspect of many systems, but it is vitally important for high temperature systems in winter months due to the temperature difference in and outside of the process system. If your process involves dryers, kilns or mills, proper insulation is something to monitor so that your operation can run smoothly.
A high temperature system contains a high temperature flow throughout its process. That flow gets carried through a baghouse. Regardless of the type of baghouse, the layout may not be ideal, if the inlet and the outlet are on the same side of the system. An ideal baghouse would have the inlet on one side and the outlet on the other. This creates a balance in flow and helps to keep the temperature consistent within the system.
If you need help insulating your system, IAC is here to help! Give us a call today at 800.334.7431 or request a quote and get your systems insulated.
However, if your baghouse already has the inlet and outlet on the same side, then proper insulation can expand the life of your system. The side of the structure that does not contain the inlets and outlets is the problem area. This area can develop corrosion and condensation due to the difference in temperature from inside and outside the system. Insulating the opposite side of the inlet and outlet area can help to limit the damage caused from the difference in temperature, ultimately prolonging the life of your baghouse.
The Importance of Baghouse Insulation Video Transcript:
Hi, I’m Luis Castano with IAC’s Tip of the Month. Today I want to talk about the importance of proper baghouse insulation, especially on high temperature systems like dryers, kilns, even mills. Okay – you’ve got high temperature flow in your process. That flow gets filtered through a baghouse, and the layout sometimes its far from ideal. Flows tend to charge to one side, in this case regardless of the type of baghouse – maybe a pulse jet or reverse air - but with the inlet and the outlet on the same side airflow tends to follow a certain pattern. It does not want to go all the way to this corner and warm it up. So, with high temperature, and cold temperature outside, you have a big difference in temperature.
Well, I have seen process baghouses without proper insulation. What happens is that it ends up causing a lot of moisture problems and extreme corrosion. I have seen process baghouses even in desert areas where for some reason the installer dosen’t think insulation is that critical, but with the temperature difference between the process and the outside you will see condensation ends up flaking and sometimes its severe enough it will cause you to surpass the limits of allowable emissions. So make sure that all corners of the baghouse are properly insulated. Also if you have the opportunity to be involved in a project with a new system, it’s much better to balance the air flows in a way that you don’t have stagnant air.
This is something IAC can help you with from the get-go on your new project. A lot of them are already installed far from ideal. Just make sure your insulation covers every corner; that you don’t have openings where rain can seep in, because you will see extreme corrosion, and that’s something to watch out for.
If you want to discuss this in more detail with one of our engineers give us a call. Thank you!
Reach out and get started on your next baghouse dust collection or ventilation project!