Static Pressure and Dust Collection - How to Optimize Performance
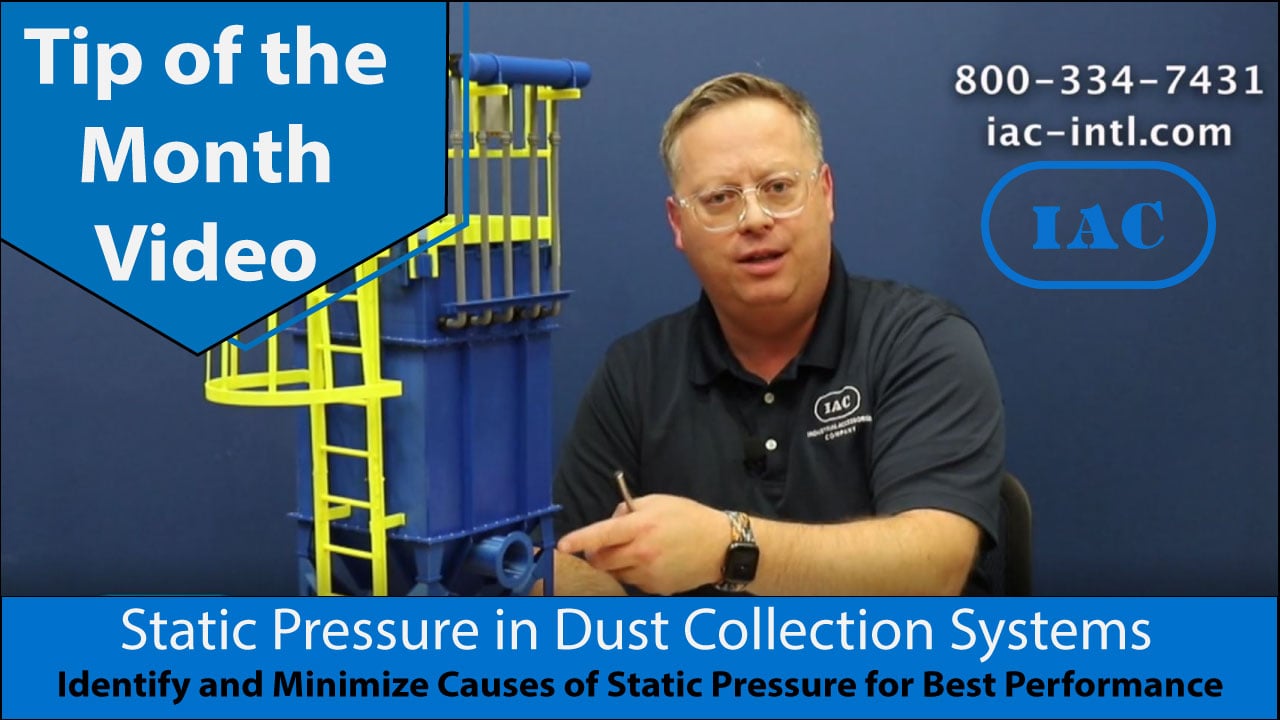
What is static pressure in a dust collector system? In terms of airflow, static pressure is a measure of the resistance that air encounters while moving through the ventilation system before and after the dust collector, which could be a baghouse, filter receiver, cyclone, or bin vent.
There are a variety of components that cause static pressure in dust collection systems. Something as simple as an elbow in a duct, to something as complex as the passing of air through a tube sheet, causes static pressure in a dust collector system. Whether the filters are clean or dirty, they impact static pressure, but the dirty filters have more resistance. When air enters the duct system through a hood or canopy, this will also cause static pressure. It's important to be aware of the static pressure in a dust collection system, and reduce or eliminate it wherever possible.
Static Pressure in Dust Collection Systems Explained
This article was created for IAC's sponsorship of the Powder and Bulk Solids Magazine 2024 Dry Pro Webinar on Dust Collection titled, | ![]() This webinar is available for viewing until January 2025. Learn more on PBS's Webinars page. |
Airflow Resistance:
Since static pressure represents the resistance that air encounters as it moves through the ducts, filters, hoods, and other components of s dust collection system, a high static pressure measurement indicates a greater resistance, which can impede the airflow and reduce the overall system efficiency.
IAC's dust collection systems are designed to minimize static pressure with smart details such as flush mounted access doors in ductwork, correctly sized ductwork, minimal use of flexible duct materials, and elbows (bends) with radiuses matched to air volume, velocity, and abrasion resistance.
Component Selection and Placement:
Understanding static pressure helps in selecting appropriate components such as filters, duct materials, and hoods. Proper placement of these components in a dust collection system is crucial to minimize pressure losses and optimize system performance.
Fan and Blower Selection and Sizing:
Static pressure is used to determine the fan or blower's capability to overcome resistance and deliver the necessary airflow to move dust laden air through the ventilation system without dust settlement and into the dust collector for filtration.
Proper fan selection and sizing are critical for maintaining the required airflow through the ventilation and dust collection system.
READ MORE ABOUT TYPES OF INDUSTRIAL FANS IN OUR KNOWLEDGE BASE
When purchasing a fan or blower, it will be rated for moving a certain amount of cubic feet of air per minute (CFM) at a given amount of static pressure. For example, the fan may be rated for 10,000 CFM at 11" of static pressure.
As a dust collection OEM since 1987, IAC's system engineers are experts at matching the correct CFM fan or blower and dust collector to your process requirements and budget.
Minimizing static pressure is an important aspect of designing a high efficiency dust collection system, yet it's easily overlooked by other suppliers because they only sell the dust collector. They don't have the engineering staff, metal fabrication facilities, or specialty industrial construction crews to offer full ventilation system design and build services (EPC). IAC's ventilation system designs minimize static pressure and maximize air flow for efficient, cost effective, high technology dust collection and air pollution control systems. Contact IAC today!
How Static Pressure Is Measured
In dust collection systems, static pressure is generally measured in inches of water, a unit which is defined by the amount of pressure (or suction) it takes to move the water level in a tube by one inch. The static pressure at any point in the system can be measured with a differential pressure gauge by connecting one port on the gauge to a component in the system and leaving the second port on the gauge open to atmosphere.
A differential pressure gauge is also used for measuring the pressure drop across a component in a system, such as the dust collector. The "+" port is connected to the upstream side of the component and the "-" port is connected to the downstream side, or the dusty air plenum and clean air plenum on a dust collector. Generally, low pressure drops across component are desirable and save energy. High pressure drops may indicate an excessive dust build up issue.
The static pressure in your dust collection system can greatly influence its efficiency. A better understanding of static pressure can help in optimizing the performance of your dust collection system, no matter how simple or complex it is, thereby ensuring a safer and cleaner working environment.
Tips for Optimizing Static Pressure
Minimize Friction
- Use smooth, properly sized ducts and elbows to minimize friction and pressure drops
Proper Component Sizing
- Ensure that filters, hoods, and other components are appropriately sized for the airflow requirements
Regular Maintenance
- Keep the system clean and well maintained to prevent dust buildup, which can increase pressure drops
Fan Speed Control
- Implement fan speed control mechanisms to adapt to varying airflow requirements and minimize energy consumption
In summary, static pressure is a key parameter in designing and operating efficient dust collection systems. By understanding its significance and how to minimize it, engineers and operators can optimize system performance, reduce energy consumption, and ensure effective dust control in industrial environments.