Smart Plant Remote Monitoring Equipment Improves Baghouse Health

When IAC’s Vice President of Engineering, Tristan Trupka, was a guest on the 174th episode of the “Dust Safety Science” Podcast, there was some discussion that IAC’s Joe Haney may also be invited to the show. As hoped, Joe joined host Dr. Chris Cloney (PEng.) for the show’s 180th episode. If you missed Tristan’s episode you can read a summary or link to that installment here.
Dr. Cloney has not only educated those in the field on combustible dust safety through his podcast, but he has also published over 15 peer-reviewed papers, spoken at events including the 2017 Explosion Safety Days in Brilon, Germany, and recently launched a dust safety magazine. This episode contains a detailed discussion regarding emerging remote monitoring technology like IAC’s Smart Plant Remote Monitoring Equipment, and though it may not seem like a part of dust safety at first glance, actually fire and explosion safety is one of the many benefits of a Smart Plant System.
Joe Haney began the show with an overview of his extensive history in the dust collection industry. As soon as his second job out of college, Joe started in sales for industrial filtration and found that the field fit him just like a perfectly sized snap band. The uniqueness of dust collection and air pollution control was so interesting, that he spent over 20 years with a baghouse company before joining IAC in early 2021. Throughout his experience, he has worked with all sorts of manufacturers, companies in the food industry, facilities with explosive dust, or any company that utilized a baghouse. He currently is IAC’s Smart Plant Product Manager. Before diving into the newest dust collection technology, Joe gives context on what changes have occurred with dust filtration over time.
In the dust collection industry, changes don’t come weekly or monthly; a lot of the technology and principles of how baghouses work are still similar to 20 years ago. Though the overall idea and methods of filtration are largely the same, with a few variations, manufacturing sites have gotten larger and the capacities and sizes of baghouses have grown to match. Some dust collection systems have become so large in size that a standard filter change out can be a Cap Ex Project, due to the number of filters and the expense. Now the newest changes in the industry are less about size and more focused on baghouse optimization, specifically by implementing Smart Remote Monitoring Technology.
What is a Smart Plant System?
IAC’s Smart Plant Remote Monitoring Equipment is designed to work with the control system for a local baghouse or dust collector and make that measurable data available 24/7 on an online portal. This technology is perfect for less-than-ideal baghouse locations, such as on top of silos, in remote locations like a fuel yard, in a small or difficult part of plant, or any area that is not connected with a central control system. Smart Plant Technology falls under the umbrella of IoT (Internet of Things) and the “Industrial Revolution 4.0,” working to connect dust collectors and collect data with sensors.
One specific example of where a manufacturer may install Smart Plant Equipment is on a bin vent on top of silo collecting cement dust. This equipment would normally need to be physically checked for information such as pressure, operation status, if the filters are cleaning, if the bin vent is emitting, etc. However, if Smart Plant Equipment was installed, it would automatically deliver these measurables to an encrypted central portal on the internet. Within this portal, users can set up notifications to be alerted via email or text message, when a measurement reads out of its set perimeters. These messages can be further customized to alert different personal, dependent on what function of the baghouse needs to be addressed. We’ve found that not only can this technology be used to improve the visibility of data, but this information also provides the ability to determine the cause of issues within dust collection systems. This provides the end user actionable information in a cost-effective way.
Effectiveness
Often facilities will choose the piece of equipment with the most frequent issues as a starting point to try the smart sensor technology. One IAC customer had a baghouse which repeatedly had high differential pressure. They couldn’t determine the cause, and their maintenance team often had to perform change outs to replace crushed filters. Once they installed an IAC Smart Plant Controller, they had more data and were able to determine the source of the issue.
The cause? Their fuel mix came from multiple sources and one of their providers supplied dirtier fuel; this shot up the pressure readings so much that the baghouse would fail. Once the problem was determined, IAC helped the customer evaluate their options in preparation for the next fuel delivery. Some of the ideas included augmenting the baghouse cleaning system or lowering the draft within system as much as possible while maintaining the carrying velocity needed in the ductwork. Neither of these solutions could have been brainstormed without knowing the source of the issue, and the source was only known because of the consistency and accuracy of data available to be analyzed. Chris pointed out that this specific customer story is a great example of effectiveness, because now the customer has switched to prevent a high differential pressure and preserve the longevity of their filters.
Efficiency
Facilities trying out Smart Plant Equipment sometimes choose at first to continue manually checking the measurements now being tracked digitally, though over time all have found consistency between the two measurements. Once proven reliable, the need for personnel to physically check data points already monitored with the Smart Plant Equipment is minimized, unless otherwise required by an entity such as state law or expectations set by corporate. Now maintenance team members are able to spend their time on more critical and valuable work on the plant, a great example of how this technology helps with facility efficiency.
Top Five Benefits
Chris took a moment to point out five features of the Smart Plant he found key:
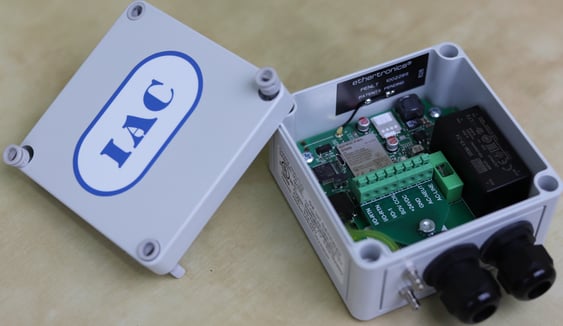
1. This technology can work for any size system from small local systems on a piece of equipment to site-wide fully-integrated systems.
2. The Smart Plant System is an industrial remote monitoring tool, so end users can monitor their equipment no matter their location.
3. Users can receive a large amount of data and involve many connection points, without the same issues that can come from the standard way of checking measurements. Manually there can be too much information at once to take in, or if employees hear the same non-critical alarm go off too frequently, they may experience “alarm fatigue” and not take action. Smart Plant technology eliminates that possibility because only the relevant personnel get notified when a measurement is out of its preset range.
4. There is the option of multiple control inputs/control systems.
5. Information comes in real time, and is consistently available because the Smart Plant is a base control system.
What Can Be Measured?
Anything that can be measured manually, can instead be collected by Smart Plant Remote Monitoring Systems. As mentioned previously differential pressure is a great and easy switch, but other data points facilities are starting to monitor digitally include:
Static pressure- Specifically with pulse jet air compressors. Compressed air pressure is what cleans the filters in a baghouse. Without proper cleaning, the pressure of a baghouse climbs until it fails. In these situations, there is often an issue with the cleaning system of the baghouse. Until recently this could only be determined by physically seeing the issue in the system or by being next to it and hearing the hiss of a failed diaphragm valve or hearing the pop of a valve not firing. However, by tracking static pressure using smart technology these issues can be identified sooner, before baghouse failure.
Vibration on a fan or fan motor- Is key for preserving fan life. Fans and fan motors shouldn’t go above a certain vibration level or the motor will not last. This can also be monitored and alerted for using the Smart Plant Monitoring System to preserve fan life.
Level detector in the hopper- An IAC customer had a hopper that didn’t function due to a jam in the airlock. IAC installed a Smart Plant Level Detector in the hopper, so now maintenance personnel will have a notification well before the issue reaches a critical level.
Incoming temperature- This is important not only for the life of filters and material being processed, but an out-of-control temperature may actually be beneficial in another area of the plant. This includes the crusher, mill, classifier, or whatever is ventilating, so long as the outlet temperature on that system can be measured as well.
Humidity- Is not a friend to dust collectors because usually the term dust collectors refers only to dry dust collection systems, not systems like wet scrubbers or mist collectors. Dust collection systems collect dry particulate before it goes into the plant or out to the atmosphere. The tricky thing with manufacturing facilities is that a lot of factory equipment is created to drive off moisture, but that moisture has to go somewhere, so it may try to enter the baghouse. Tracking humidity with Smart Monitoring Equipment creates a much better chance to catch that problem early and ensure a longer filter-life.
The Whole Picture of Baghouse Health
Throughout their discussion, Chris and Joe formulated an analogy comparing the upkeep of a baghouse’s health, to the upkeep of a person getting a physical, and how new technology impacts what that can look like. Some baghouse readings like differential pressure are as key to the health of a baghouse as getting looked at with a stethoscope is key to a physical. Both tools help create an overall snapshot of health. This three-part analogy highlights how information and technology make that snapshot a larger, clearer picture.
1) If a doctor didn’t use a stethoscope in the exam, it would be unusual and the patient should get a different doctor. If no baghouse measurements are taken, it would be impossible to maintain the equipment.
2) If the doctor is able to take measurements periodically over time, that is the standard procedure and works at an okay level. This is the current, typical way baghouse health is measured and maintained.
3) However, if the doctor had access to stethoscope measurements taken consistently and frequently, recorded before the appointment, then all that would be left would be to formulate a plan. This scenario would be the most beneficial to the doctor and patient, and represents the significant assistance a Smart Plant can bring to a manufacturer. It provides the advantage of real time data collection that can be analyzed, to prevent issues from happening and extend the lifetime of a baghouse. Smart Plant Equipment provides data over time available for viewing anywhere with internet access, without gauges being physically checked; it’s the possibility to work proactively rather than reactively
Joe then simplifies the three main areas of a dust collector’s health and why they may fail:
1. Thermal/temperature – Potential failures include fires or explosions, which currently happen multiple times a week in facilities across the U.S.
2. Chemical – Failure can occur if the dew point reaches a level where water droplets form on the filters, this can be avoided with a humidity sensor in the gas stream.
3. Mechanical – These failures are similar to the routine replacements of car tires; some items just have a certain lifetime. The act of cleaning filters, ages filters. It’s aggressive in a pulse jet system, so the more a plant can do to minimize cleaning cycles the better.
All three of these areas can now be more closely monitored to preserve baghouse health with Smart Plant Technology.
IAC recently shipped a baghouse to a customer who previously had 12 baghouses. All of their baghouses cleaned on “time,” or operated so the cleaning system fired off a cycle where every X number of seconds and once manifold pressure was recovered, the filters cleaned again. This cycle was consistent throughout the whole operation of the baghouse, and this was a fine approach that likely kept low pressure in the baghouse. That being said, the goal was to make the filters last as long as possible and keep maintenance working on more critical projects, so the customer decided it was worth determining if their baghouse actually needed to be cleaned as frequently as it was. After a little convincing this facility installed IAC’s Smart Plant Equipment and changed their system to clean on demand determined by the baghouse pressure. Now it is set up to automatically start cleaning at a differential pressure of five and stop once the differential pressure has been reduced by a half inch and then wait until the baghouse is at the highest set point to be cleaned again. The methodology and advise used at this plant is not new, but now there’s much more data to support it and technology to make implementing it easier. This specific customer was able to reduce their cleaning cycles by 80-90% because they were not required to maintain that pressure. This will likely extend their filter life out a year.
Work Smarter, Not Harder
The Smart Plant System helps identify warning signs much earlier than possible before and reduces the likelihood of dangerous conditions like fires and explosions. Even trained personnel at baghouses with burst panels for explosion mitigation may be unaware that an event caused the burst panels to be released. These plants may have an unaddressed explosive condition for hours or days. Smart Plant Remote Monitoring connected to a relay sensor, would provide an immediate notification that this occurred and allow plants to prioritize safety.
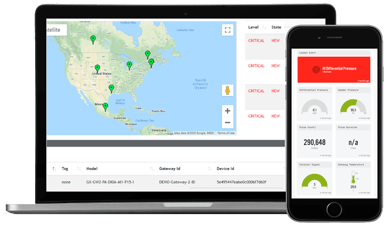
This equipment ties all of a plant’s systems together, not only fire and explosion safety systems, but other smart systems and more, to create a dashboard where all the data is accessible. Alerts are customizable and managed by the plant to always involve the right people and avoid alarm fatigue. While there could be a learning curve to find the parameters and balance that work for your equipment, staff, and local permits, IAC is happy to help with any questions that may arise.
One of the goals with this new innovation is to keep plant operations cost effective. Facilities can start small with a static pressure or differential pressure gauge to see the results, and then add more Smart Equipment from there. The other goal is to simplify installation to make everything “wireless,” making installs easier. This frees up time allowing personnel to instead analyze their new influx of data and better understand their facility’s problems. Want a measurable you don’t see IAC mentioning? We can make it happen. IAC loves to collaborate with customers to find the solutions for your specific plant. IAC’s Smart Plant Remote Monitoring Equipment is the most well-rounded way to keep your baghouse healthy.
Listen to the full podcast episode here.